管道化學(xué)清洗除垢詳解(點(diǎn)擊進(jìn)入)
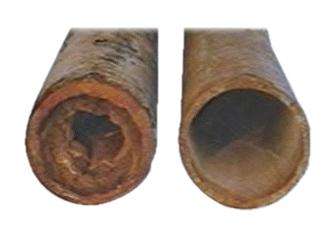
工業(yè)管道化學(xué)清洗通用工藝
1適用范圍
1.1本通用工藝適用于工業(yè)金屬管道工程中設(shè)計(jì)文件規(guī)定的需要進(jìn)行化學(xué)清洗的管道施工,。
1.2本通用工藝不適用于工業(yè)金屬管道工程中用水沖洗和油清洗的施工。
2引用(依據(jù))文件
2.1《工業(yè)金屬管道工程施工及驗(yàn)收規(guī)范》 GB50235-97
2.2《石油化工鋼制管道工程技術(shù)規(guī)程》 SHJ517-91
3施工準(zhǔn)備
3.1材料準(zhǔn)備
3.1.1所有用于工業(yè)管道化學(xué)清洗的化學(xué)清洗藥品必須具有出廠質(zhì)量合格證明書(shū),,其化學(xué)成分和特性必須符合有關(guān)標(biāo)準(zhǔn)的要求,。
3.1.2用于現(xiàn)場(chǎng)臨時(shí)接管的管子及其配件、材料宜采用不銹鋼材料或塑料材料,。
3.1.3用于現(xiàn)場(chǎng)盛接清洗化學(xué)藥品的容器應(yīng)采用不銹鋼或塑料制品,。
3.2設(shè)備機(jī)具
3.2.1設(shè)備:耐酸泵、不銹鋼水槽,、水泵,、空壓機(jī)、清洗質(zhì)量檢查用黑光燈,、YX-125攜帶式螢光探傷儀(功率125W)等,。
3.2.2用于浸泡法和擦洗法使用的工器具有塑料桶、盆,、不銹鋼刷,、毛刷以及必備的勞動(dòng)保護(hù)用品。
3.3作業(yè)條件
3.3.1試壓已經(jīng)結(jié)束,,并辦理工序交接,。
4施工工藝
4.1施工程序見(jiàn)圖4.1
4.2.安裝臨時(shí)管線(需要循環(huán)酸洗時(shí))
4.2.1臨時(shí)配管口徑,原則上主管直徑不得小于100mm,,支管直徑與正式管徑相同,;
4.2.2布置好放空線和排疑線
4.2.3臨時(shí)配管應(yīng)根據(jù)實(shí)際需要加臨時(shí)支架;
4.3 預(yù)清理
管道內(nèi)表面有明顯油斑時(shí),,不論采用何種酸洗方法,,酸洗前應(yīng)進(jìn)行必要的預(yù)除油處理,一般采用5%的碳酸鈉溶液清除油污或用四氯化碳(或三氯乙烯)進(jìn)行脫脂處理,。同時(shí)檢查焊縫質(zhì)量,,如有較大焊瘤及焊渣等,應(yīng)加以處理,。
4.4 酸洗
4.4.1可采用槽浸法或系統(tǒng)循環(huán)法進(jìn)行酸洗,,酸洗液應(yīng)按規(guī)定的配方按順序進(jìn)行配制,并應(yīng)攪拌均勻,。酸洗液,、中和液及純化液的配方,,當(dāng)設(shè)計(jì)未規(guī)定時(shí)可按表4.4.1-1和表4.4.1-2的規(guī)定配制使用。
表4.4.1-1 碳素鋼及低合金鋼管道酸洗液和鈍化液配方
濃
液 |
循 環(huán) 法 |
槽 式 浸 泡 法 |
||||||||||||||||||
配方一 |
配方二 |
配方一 |
配方二 |
|||||||||||||||||
名稱(chēng) |
濃度 % |
溫度℃ |
時(shí)間 min |
PH值 |
名稱(chēng) |
濃度 % |
溫度 ℃ |
時(shí)間 min |
PH值 |
名稱(chēng) |
濃度 % |
溫度 ℃ |
時(shí)間 min |
PH值 |
名稱(chēng) |
濃度 % |
溫度 ℃ |
時(shí)間 min |
PH值 |
|
酸洗液 |
鹽酸 |
9~10 |
常溫 |
45 |
|
鹽酸 |
12~16 |
常溫 |
120 |
|
硝酸NBOS-PC400 (日本) |
20~30wt |
40~60 |
|
|
鹽酸 |
12 |
常溫 |
120 |
|
烏洛托品 |
1 |
|
烏洛托品 |
0.5~0.7 |
烏洛托品 |
1 |
||||||||||||||
中和液 |
氨水 |
0.1~1 |
60℃ |
15 |
>9 |
碳酸鈉 |
0.3 |
常溫 |
|
|
|
|
|
|
|
氨水 |
1 |
常溫 |
5 |
|
鈍化液 |
亞硝酸鈉 |
12~14 |
常溫 |
25 |
10~11 |
亞硝酸鈉 |
5~6 |
常溫 |
動(dòng)態(tài)30+情態(tài)120 |
7.2~7.3 |
|
|
|
|
|
亞硝酸鈉 |
10~15 |
常溫 |
15 |
10~1 |
氨水 |
1 |
|
|
|
|
|
表4.4.1-2 不銹耐酸鋼管道酸洗和鈍化液配方
溶 液 名 稱(chēng) |
配方一 |
配方二 |
|||||||
名 稱(chēng) |
濃度% |
溫度℃ |
時(shí)間min |
名 稱(chēng) |
體積比例% |
溫度℃ |
時(shí)間min |
||
酸 洗 液 |
氫氟酸(HF) |
1~5 |
|
|
硝酸 (HNO3) |
15 |
49~60 |
26 |
|
硝酸鈉 (NaNO3) |
10~20 |
常溫 |
15 |
氫氟酸(HF) |
1 |
||||
水(H2O) |
余量 |
水(H2O) |
84 |
||||||
中 和 液 |
碳硝酸(NaCO2) |
5 |
常溫 |
6~10 |
|
|
|
|
|
鈍 化 液 |
硝 酸 (HNO3) |
30 |
常溫 |
46 |
|
|
|
|
4.4.2系統(tǒng)循環(huán)法即用酸泵向管內(nèi)邊灌酸液,,邊排空氣,,排凈空氣后再進(jìn)行循環(huán),酸洗的操作溫度和持續(xù)時(shí)間,,應(yīng)根據(jù)銹斑去除情況而定,,一般情況持續(xù)6-8小時(shí),酸洗液溫度為70℃左右,。
4.4.3酸洗過(guò)程中,,應(yīng)定期分析酸洗液的成分并及時(shí)補(bǔ)充新液,當(dāng)除銹效果明顯下降時(shí),,應(yīng)予以更換,。
4.5中和清洗:
酸洗排凈后,接上中和液膠管,,用泵動(dòng)態(tài)進(jìn)行管內(nèi)殘存酸液的中和。在排放口用PH試紙檢查,,當(dāng)溶液呈中性或弱堿性時(shí),,即停止中和。
4.6鈍化
酸洗,、中和合格后,,接上鈍化液膠管,啟動(dòng)泵向管內(nèi),。灌送鈍化液,,邊灌邊排空氣,使鈍化液在管內(nèi)循環(huán)半小時(shí)后,,再靜態(tài)2小時(shí)后排放干凈
4.7 水沖洗
鈍化后,,開(kāi)啟 水泵用潔凈水沖洗循環(huán)系統(tǒng)。
4.8干燥:水沖洗后,,立即用干燥氣吹掃循環(huán)系統(tǒng),,直至管道內(nèi)殘液全部排凈。
4.8.1水沖洗合格后,,用干燥無(wú)油空氣或氮?dú)鈴氐状蹈晒軆?nèi)壁,。碳鋼管內(nèi)壁呈銀灰色認(rèn)為合格。
4.8.2在完成系統(tǒng)吹掃干燥后,,應(yīng)在短時(shí)間內(nèi)拆除臨時(shí)管線,,并將拆除的管道附件恢復(fù)。如果距試,、開(kāi)車(chē)時(shí)間較長(zhǎng),,待管道系統(tǒng)恢復(fù)后,,在系統(tǒng)內(nèi)充0.07MPa的 氮?dú)鈱?duì)管道系統(tǒng)進(jìn)行氮封保護(hù)。
4.9對(duì)于小型管段,,管件等可采用浸泡法清洗,,清洗時(shí)將管段、管件直接放入各溶液槽中,,其步驟與循環(huán)清洗一樣,,經(jīng)酸洗,中和,、鈍化,、水洗、干燥后組裝,,根據(jù)需要進(jìn)行充氮保護(hù),。
5質(zhì)量標(biāo)準(zhǔn)
5.1管內(nèi)表面或清洗件表面無(wú)鐵銹和氧化斑跡,無(wú)雜質(zhì),、水垢并呈金屬光澤,。
5.2 酸洗后的管道以目測(cè)檢查法以管道內(nèi)壁呈金屬光澤為合格。
5.3中和后,,溶液的PH值應(yīng)為9-9.5,。
5.4鈍化的質(zhì)量以蘭點(diǎn)檢驗(yàn)法檢查鈍化膜致密性。用檢驗(yàn)液一滴點(diǎn)于鈍化表面,,15min內(nèi)出現(xiàn)的蘭點(diǎn),,少于8點(diǎn)為合格。蘭點(diǎn)檢驗(yàn)液的配方,,見(jiàn)表5.4
表5.4 蘭點(diǎn)檢驗(yàn)液配方
藥劑名稱(chēng) |
鹽酸 |
硫酸 |
鐵氰化鉀 |
蒸餾水 |
%含量 |
5 |
1 |
5 |
89 |
6施工注意事項(xiàng)
6.1為獲得良好的清洗質(zhì)量,,使化學(xué)清洗溶液在一定流速下對(duì)管內(nèi)壁產(chǎn)生沖蝕最佳效果,應(yīng)選用大揚(yáng)程大流量耐蝕泵使溶液在一定壓力下對(duì)整個(gè)回路管道進(jìn)行循環(huán)清洗,。其清洗簡(jiǎn)易流程見(jiàn)附圖1,。
6.2酸洗時(shí),管內(nèi)排空很重要,,一定要使管內(nèi)不產(chǎn)生氣囊,,否則該處鐵銹洗不到,會(huì)嚴(yán)重影響酸洗質(zhì)量,。
6.3酸洗液和鈍化液要經(jīng)常檢查其濃度,,應(yīng)始終保持規(guī)定的濃度,否測(cè)影響處理效果,。
6.4應(yīng)嚴(yán)禁酸液與中和液,、鈍化液相混合,尤其鈍化液,,否測(cè)將產(chǎn)生有毒的二氧化氮?dú)怏w,,影響操作人員身體健康,。
6.5酸洗完成后應(yīng)隨即進(jìn)行鈍化,鈍化完畢隨即密封,,中途不能停頓,,以免管內(nèi)再次氧化。
7成品保護(hù)
7.1所有清洗合格的管道及其附件不得損壞,,如不能及時(shí)進(jìn)行管道系統(tǒng)復(fù)位,,必須用塑料布進(jìn)行包封。
7.2復(fù)位后,,要求氮封時(shí),,應(yīng)及時(shí)在系統(tǒng)內(nèi)充氮?dú)猓⑾到y(tǒng)內(nèi)空氣置換完,,每系統(tǒng)應(yīng)設(shè)置兩塊以上的壓力表監(jiān)視氮封壓力,。為保證氮封效果,應(yīng)設(shè)立專(zhuān)人進(jìn)行定時(shí)檢查,,當(dāng)系統(tǒng)內(nèi)氮?dú)鈮毫Φ陀?/span>0.05MPa時(shí),,應(yīng)及時(shí)補(bǔ)充氮?dú)猓⒈WC氮?dú)鈮毫υ?/span>0.07~0.1 MPa,。
8質(zhì)量記錄
工序交接記錄
管道吹洗(脫脂)記錄
|
附圖1:循環(huán)清洗簡(jiǎn)易流程